SAFETY & OCCUPATIONAL HEALTH
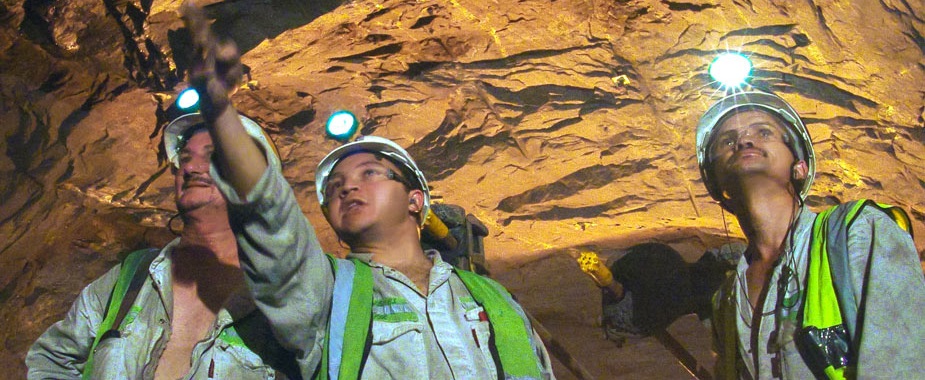
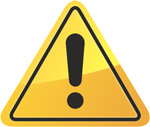
SAFETY & OCCUPATIONAL HEALTH ARE PRIME ELEMENTS OF THE VEDANTA SUSTAINABILITY ASSURANCE PROGRAMME (VSAP) AND EVERY MEMBER OF THE WORKFORCE IS EDUCATED AND ENCOURAGED TO EMBRACE SAFETY WHOLEHEARTEDLY.
Our products help shape the destiny of nations, but it is our workforce that has allowed us to become one of the largest metals & mining company on the planet. We believe that long-term success is only possible if each one of our employees and workers is able to return to their families safely at the end of the day. Their safety and well-being drives our performance. Health and safety of our workforce is therefore a material issue for us.
APPROACH
We are building a positive safety culture at Vedanta where employees get to perform to their peak potential in a safe environment and where they feel part of the safety solutions. A system has been put in place to ensure higher ownership and accountability of safety across the organisational hierarchy. Safety is discussed at senior leadership meetings and incidents fully investigated.
The message from our Board and Senior Leadership is very clear – we will continue to operate in a manner that puts safety first. To ensure that the organisation lives up to those expectations, we have a comprehensive group-level HSE policy that seeks to embed safety as a value across our operations. This policy is supported by several management and technical standards that seek to guide our workforce into implementing safe operations.
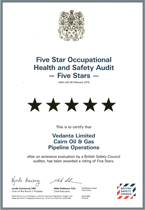
SAFETY HIGHLIGHTS
921,550
MAN-HOURS OF TRAINING ON SAFETY
100%
PERIODICAL MEDICAL EXAMINATION
LOST TIME INJURIES FREQUENCY
RATE REDUCED FROM
RATE REDUCED FROM
0.39 IN FY 2016-17 |
TO | 0.34 IN FY 2017-18 |
STERLITE COPPER RECEIVED
THE BRITISH SAFETY COUNCIL
THE BRITISH SAFETY COUNCIL
SWORD OF
HONOUR
HONOUR
ZERO HARM CULTURE
THE IMPORTANCE OF ACHIEVING A ZERO-HARM WORKPLACE HAS BEEN PROMOTED IN ALL OUR GROUP COMPANIES.
THIS ASPIRATION IS DRIVING A CULTURAL SHIFT, WITH AN EMPHASIS ON A SYSTEMIC RISK-BASED APPROACH, CLEAR EXPECTATIONS FROM OUR LEADERSHIP TEAM, AND BENCHMARKING WITH GLOBAL STANDARDS.
Our Board-Level Sustainability Committee, chaired by the Board's senior independent director, and our Executive Committee, chaired by our CEO, regularly review our safety performance and share recommendations.
For a culture of safety to gain permanence, it needs to permeate across every level of the organisation. This year, we continued to enthuse, educate and encourage every member of our workforce to embrace safety as a value and managers at all levels were made accountable for ensuring safe performance. Safety & Occupational Health is a mandatory module in our induction and refresher training programme, and periodic workshops are conducted to enhance safety awareness and knowledge among employees and contractors.
Despite our consistent efforts to strengthen safety, the number of fatalities this year increased. This is unacceptable to us, and is a matter of great concern and regret for the entire Vedanta Group. We have analysed the root causes of these incidents and have come up with definitive steps to stem and reverse this trend.
SAFETY OVERHAUL AT VEDANTA
MAIN AREAS OF INTERVENTION
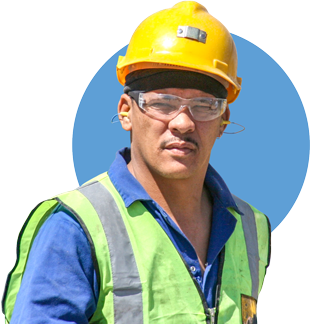
HIRED EXPERTS TO DRIVE INTERNATIONAL SAFETY PRACTICES
Global experts on safety will drive international safety practices at the unit and regional level. 11 experts have been brought on-board.
REDESIGNED THE HSE ORGANISATION TO DRIVE SAFETY PERFORMANCE
Appointed Chief Health & Safety Officers and Chief Environment Managers to enhance engagement with businesses on safety. Also appointed site-based line leaders to implement effective safety controls. Experienced employees were given the responsibility at 'regional' levels to drive safety performance and ensure that knowledge sharing and lessons learnt are adequately implemented across all sites.
ADDED NEW SAFETY STANDARDS
Apart from the six existing standards, new standards on Machine Guarding, Cranes and Lifting, Molten Metals, and Pit, Dump and Stockpile Safety were added. All sites are expected to strictly adhere to the provisions of these standards and will be audited against their implementation in our annual VSAP audit.
APPOINTED ZONE-WISE MANAGERS
To ensure that every area in our operations adheres to all principles of safe operations, we have appointed zone-wise managers who are accountable for the overall safety of their areas.
INTRODUCED SAFETY AS COMPETENCY METRIC TO EVALUATE EMPLOYEE PERFORMANCE
Safety competency was introduced as an indicator in the KPI of each employee. This will help us track employees on their ability to follow safe behaviour as well as keep themselves abreast of safe work practices through training and capacity building programmes.
SAFETY PERFORMANCE
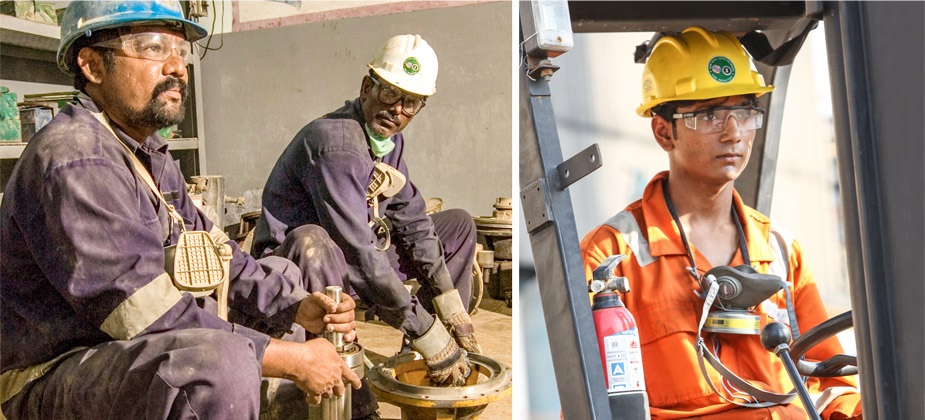
Safety incidents in the areas where we put our focus have reduced over a 3-year period. This can be seen in the LTIFR, which has reduced from a high of 0.54 in FY 2013-14 to 0.34 in FY 2017-18. Against the target to achieve more than 75% in six safety
performance standards, average safety score across all our businesses increased from 52% to 60%.
However, this positive trend has been marred by an uptick in the number of fatalities experienced in the reporting period. After seeing a downward trend in the number of fatalities in the previous years, our operations experienced 9 fatalities this year. Two-thirds of these fatalities occurred in areas that were outside of the focus of our 'fatal risk standards campaign'.
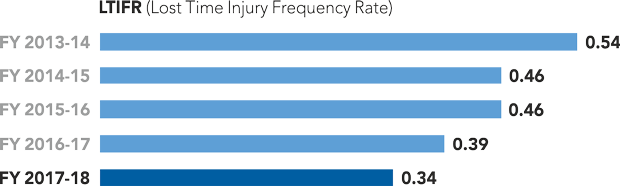
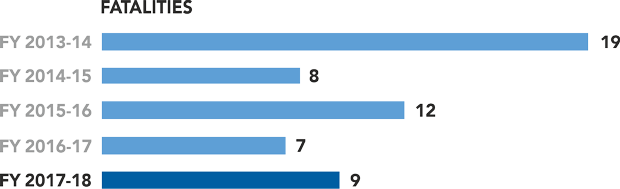
In one way, it is an affirmation of our approach. However, it also tells us that safety is all-inclusive, and we need to remain ever vigilant. We have introduced additional safety standards considering these events, and we are also conducting trainings and programmes for our workforce so that they can identify, prevent, and manage safety risks irrespective of the presence of a standard.
LAST YEAR,
WE PROVIDED
WE PROVIDED
984,137
MAN-HOURS OF HSE TRAINING, WHICH INCLUDED
MAN-HOURS OF HSE TRAINING, WHICH INCLUDED
89,567
MAN-HOURS FOR
THE EMPLOYEES AND
MAN-HOURS FOR
THE EMPLOYEES AND
894,570
MAN-HOURS FOR CONTRACTORS
& THIRD-PARTY WORKERS
MAN-HOURS FOR CONTRACTORS
& THIRD-PARTY WORKERS

MBRD
Making Better
Risk Decisions
Making Better
Risk Decisions
CRI
Critical Risk
Identification
Critical Risk
Identification
Training programmes such as 'Making Better Risk Decisions' (MBRD) and 'Critical Risk Identification' (CRI) are among the key programmes through which we have collectively imparted over 921,550 hours of safety training to our employees, contractors, and third-party vendors. We also regularly share learnings from the investigations to our high potential and fatal safety incidents.
KEY INITIATIVES
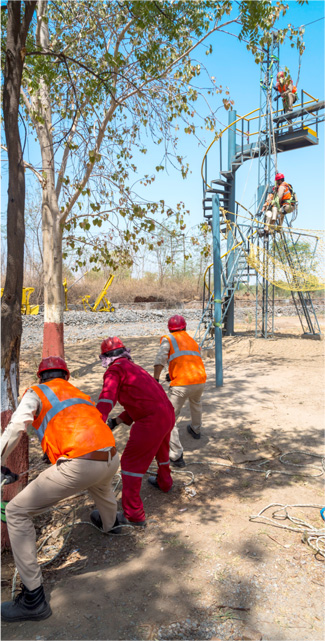
OCCUPATIONAL HEALTH AND SAFETY AUDIT – CAIRN

OCCUPATIONAL HEALTH AND SAFETY AUDIT – CAIRN
With the objective of validating effective implementation of safety programmes and strengthening workplace safety, Cairn Oil & Gas roped in British Safety Council to conduct a health and safety audit. The Five Star Audit process focused on the key aspects of managing health and safety in the workplace and offered a structured path for continual improvement towards best practice status.
Throughout the audit, five best practice indicators, including leadership, stakeholder engagement, risk management, organisation health and safety culture, and continual improvement, were evaluated. Cairn achieved an audited score of 92.96%, equating to five stars.
GOOD HOUSEKEEPING LEADS TO SAFER WORKPLACES

GOOD HOUSEKEEPING LEADS TO SAFER WORKPLACES
Housekeeping is crucial to workplaces as it helps prevent injuries and improves productivity. In FY 2017-18, we launched the '5S Housekeeping Programme', with a goal to achieve a score of 90% in housekeeping audit across all of our assets. The thinking was very clear – bad housekeeping is one of the primary reasons why accidents take place. If we are able to systematically improve housekeeping, then we are likely to see a reduction in safety incidents.
During the reporting period, we have been able to improve the 5S score from an average of 65 at the beginning of the year to an average of 74, and we hope to achieve a score of 90 by the close of the next fiscal year.
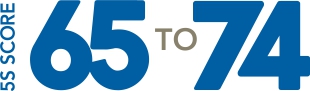
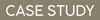
BEING SAFE - A STEP TOWARDS ATTAINING 'NO UNSAFE ACT'
With more than 10,000 contract employees working on various sites in Hindustan Zinc, propagating safe work practices to everybody is no mean feat. While stringent safety procedures play a decisive role, actions to elicit individual buy-in can go a long way in creating positive & safe outcomes.
Multiple outreach mechanisms were developed to create
self-awareness for the overarching need to remain safe.
SAFETY OWNERSHIP
PROMOTING SAFETY TO MASSES
CATCHING THEM YOUNG
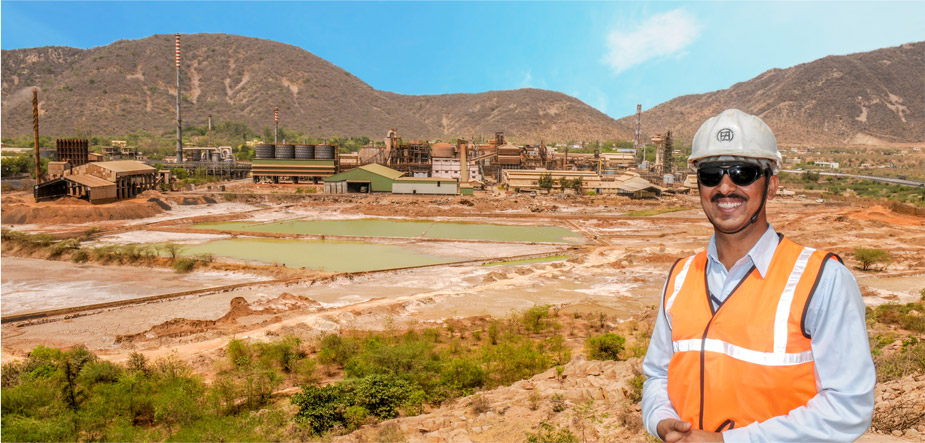
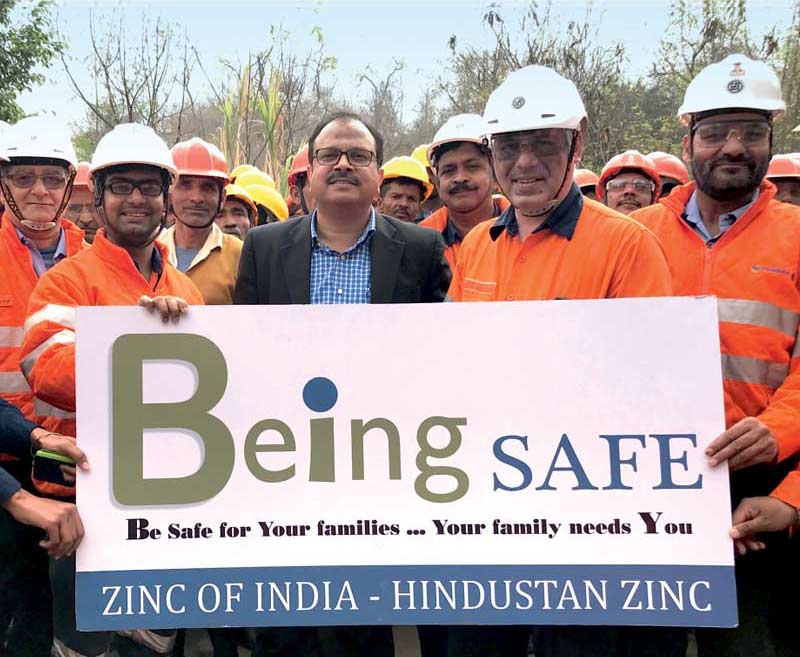
SAFETY OWNERSHIP
A scientifically designed interactive project, the objective of 'Being Safe' is to reduce the mental stress of employees and help them realise the importance of safety for themselves and their families. The project used several engagement tools, such as informal interactions, screening of specially crafted films on safety and meditation sessions to help employees imbibe safety as a value. Post-film
interactions with the employees brought forth several examples in the form of case studies or personal incidents that put a spotlight on how safety is
compromised knowingly/unknowingly, at work or away from work. Each attendee was asked to pledge to follow the path of Being Safe henceforth
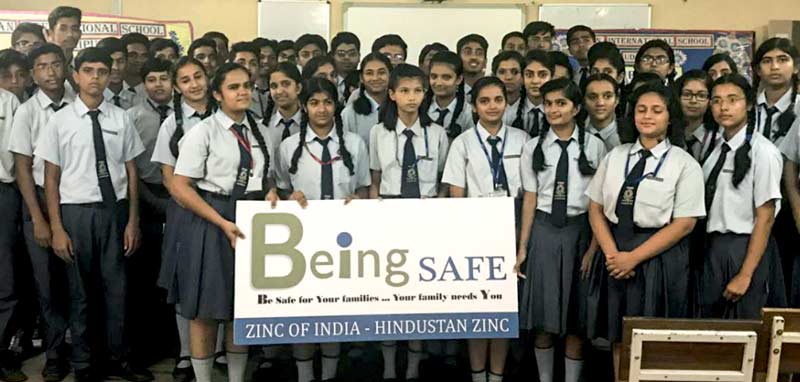
CATCHING THEM YOUNG
Extending 'Being Safe' to children, workshops were conducted for school
students of Rajasthan where over 200 students pledged for being safe and
conveyed the same to their parents and extended family members.
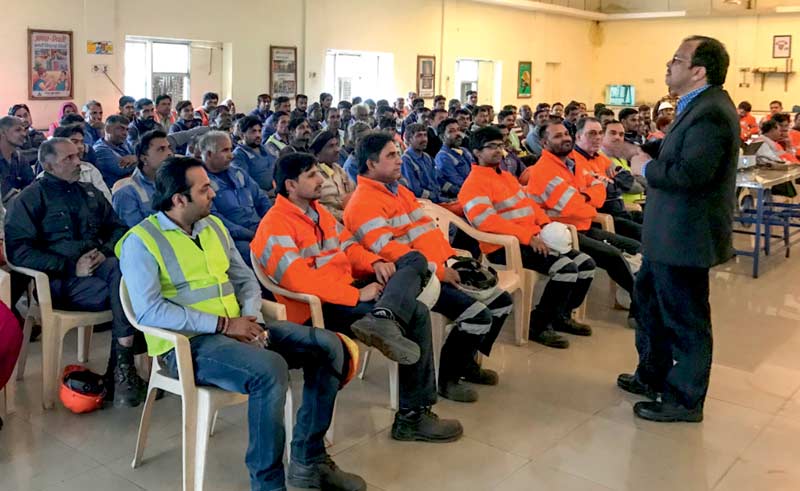
PROMOTING SAFETY TO MASSES
Conceptualised as part of our communication project, Being Safe workshops have touched many families through on-ground interactions. With the aim to promote safety beyond the boundaries of Hindustan Zinc, among the citizens of Rajasthan, a new initiative titled – 'Be Safe' was launched in association with All India Radio (AIR) Rajasthan. This 5-minute programme is broadcast daily by AIR and reaches the masses in urban and rural Rajasthan, motivating self and the families to remain safe.