|
SAFETY |
CAPABILITY BUILDING |
Capability building is core to our safety strategy. We follow an integrated approach to build safety leadership competencies at all levels of the organisation and host training programmes across the year. |
|
Firefighting Training |
During the reporting period, 27 participants, 19 workmen from API Nalgonda Plant and 8 workmen from API Srikakulam Plant, underwent a two-month course on basic firefighting at GMR Aviation Academy. Post completion, these workmen have been deployed at their respective units as Firemen. |
They are performing the following duties under the leadership of the Unit SHE team and the Fire Officer: |
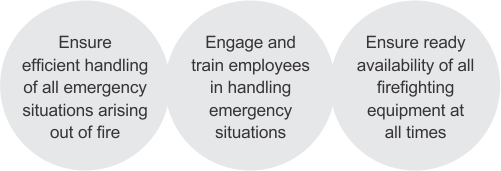 |
Besides training, we also conduct mock fire drills. 102 such drills were conducted in FY14 and 121 drills were conducted in FY15. |
|
|
Strategic Business Partner Training |
To cascade safety beyond the physical boundaries of our organisation, we also extend safety training to our Strategic Business Partners (SBP). |
61 professionals from 30 SBPs were trained in FY14 in areas such as: |
|
|
Contractor Safety
Management Training |
All contractors undergo safety induction training. All contract workmen are briefed on general safety prior to entering the site. They are also trained in job-specific safety before commencing work. Contractors are also requested to participate in safety meetings. They are also a part of our various safety awareness and promotion schemes being implemented on the site. |
2,806 employees of Dr. Reddy's have been trained in
contractor management safety till FY15. |
In FY14, 5,297 contractors
were imparted training
whereas in FY15, 3,744
contractors were trained. |
|
|
|
First Aid Training |
725 people underwent first aid training
in FY14 and 923 people underwent this
training in FY15. |
Tool Box Talks are conducted on a
regular basis to ensure that safety
occupies a top-of-mind position. Role
Based Training Module (RBTM)
empowers the individuals to turn their
safety intentions into productive practice. |
|
|
The Safety Star Caps Programme |
The Backbone of Good Safety Governance |
|
Safety Star Caps is a unique initiative introduced with an objective to empower shop floor employees in decision making, decentralise ownership and enable cross functional collaboration to enhance safety
of the organisation. |
At Dr. Reddy's, STAR is defined as: |
 |
ituation |
|
To understand the current situation, opportunities and constraints that are existent at the work place. |
|
 |
ask |
|
Know what are the tasks that are relevant to achieve team goals. |
|
 |
ction |
|
Understand what actions are necessary to improve the current situation / achieve the team goals. |
|
 |
esult & Review |
|
Determine what results are achievable on taking the correct actions and review the actual outcomes. |
|
|
|
The guiding philosophy of STAR model is to propagate situational leadership, where the role and accountability are clearly defined. |
STAR is participatory in nature and involves shop floor employees in solving problems and bringing about continuous improvement at their workstations. The uniqueness of the model is that it encourages employees to bring about these improvements in functions outside their core areas. |
|
Roles and Responsibilities of a Star Cap |
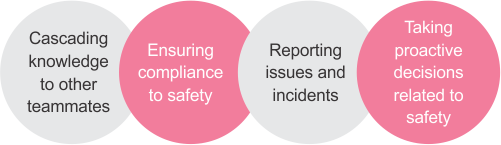 |
The functional team at the site supports the Star Caps and works closely with them to implement relevant projects. |
|
|
Who is a Star Cap? |
Start Caps are team members who voluntarily takes up additional responsibilities for their teams for a specific period (about 6 to 12 months) in addition to their day-to-day deliverables on the shop floor. They undergo intensive training in safety and is awarded a Star Cap at the end of the training. |
|
Star Caps - A Growing Tribe |
In 2015, 219 Star Caps across 6 units were selected and trained. These included workmen, chemists and SMT technical trainees. The plan is to train around 150 Star Caps in FY16. |
Number of Safety STAR CAPS Trained |
|
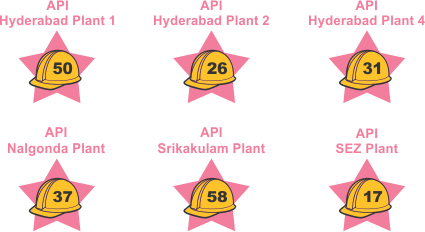 |
|
|
|
|
|