|
SAFETY |
STANDARDISED PROCESSES |
Our employees follow a six-step process whenever they spot a violation of Standard Operating Procedure: |
|
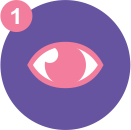 |
 |
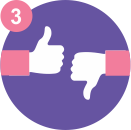 |
Observe, decide, stop
the unsafe act (safely) |
Comment on safe behaviour |
Discuss consequences. Evolve a safer way to do the job |
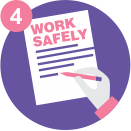 |
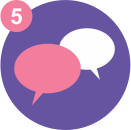 |
 |
Get an agreement to work safely |
Discuss other safety issues |
Thank the employee |
|
|
Safety Protocols |
The Backbone of Good Safety Governance |
|
Fool-proof procedures and well-thought out methods to avoid injuries are a must to achieve the safety goals of any organisation. At Dr. Reddy's, there are defined processes and protocols to be followed in each unit and zone to ensure workplace safety. |
|
Lock Out Tag Out (LOTO) |
We deploy LOTO to ensure that dangerous machines are properly shut off and not restarted prior to the completion of maintenance or servicing work. All hazardous power sources and material flow outlets are isolated and rendered inoperative before commencing the repair procedure. |
LOTO is performed to prevent injury to personnel or damage to property and or environment by the unexpected release of energy or materials. |
|
|
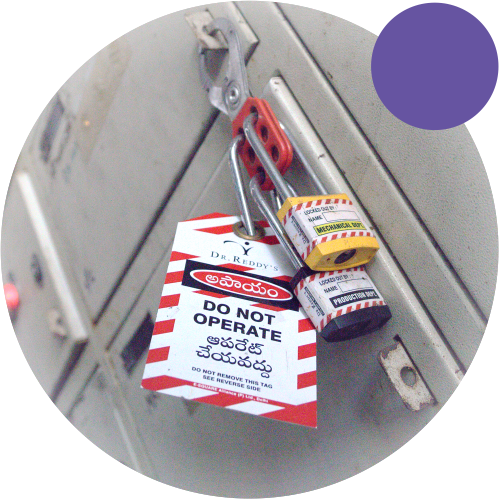 |
|
|
The following standards and procedures are followed while undertaking LOTO: |
Process isolation |
Electrical safety
management |
'Permit to work'
procedures |
Confined space
entry precautions |
Hazard identification and risk
mitigation - job safety analysis |
Safety principles
and SHE policies |
|
|
Permit to Work System |
It is a formal, documented safety procedure that forms a critical part of the safe working system. It ensures that: |
 |
All necessary actions are taken before, during and after particularly high risk work. |
|
 |
All the risks have been identified. |
|
 |
All the precautions have been put
in place. |
|
 |
Appropriate information has been communicated to all relevant parties. |
|
|
|
Job Safety Analysis (JSA) |
JSA is a method for developing a job procedure that lists all the steps of the job and describes a safe way to do the job. |
It is a way of planning a job by: |
Listing the steps in the job - Standard Operating Procedure (SOP) |
Identifying the possible hazards in the job |
Describing the recommended safe way to do the job in order to prevent incidents and injuries |
Anticipating what might go wrong and devising back-up controls |
|
Keeping in mind |
 |
Causes of past injuries |
|
 |
Other work in progress near the work area |
|
 |
Legislation or regulatory requirements |
|
 |
Manufacturer's instructions for equipment |
|
|
|
|
|
|
Process Safety Management (PSM) |
PSM is directed towards controlling hazards related to chemical and pharmaceutical processing that can: |
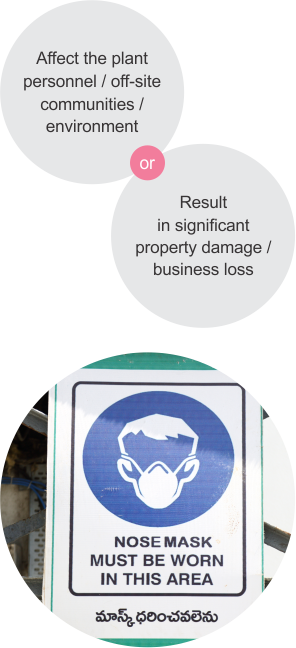 |
|
|
We implemented four important elements of PSM under this workstream: |
 |
Process Safety Information (PSI) |
|
PSI provides foundation for identifying & understanding the hazards involved and forms the basis for further PSI efforts. |
|
|
 |
Process Hazards Analysis (PHA) |
|
PHA focuses to: |
|
a. |
Identify hazard materials
and hazardous processes |
|
|
c. |
Provide a framework for understanding the hazardous events and responses to them |
|
b. |
Identify known and
unknown hazardous events |
|
|
d. |
Identify actions to eliminate and/or reduce risks involved with each hazard |
|
|
|
|
 |
Management of Change (MOC) |
|
We believe that all process & facility changes must be thoroughly reviewed before being implemented. MOC is a systematic procedure for the review of changes (including subtle changes) to the documented process technology or facilities to spot and eliminate potential hazards from being introduced in the new system. |
|
|
 |
Pre-Start Up Safety Review (PSSR) |
|
PSSR provides a final check of new and modified equipment / facilities / processes and helps confirm that all appropriate elements of process safety have been addressed satisfactorily and the facility is safe to operate. |
|
|
These elements of PSM are implemented diligently to eliminate the incidents related to processes or reduce high risks by means of controls. |
|
|
|
|
|
|
|
|