Improving productivity of material at
Dr. Reddy's is more than just making
profits, it underpins our efforts to make
medicines accessible and affordable for patients across the world. |
Material productivity of identified
products is improved by mapping the
material flow and identifying stages with
yield loss. Every stage is analysed for
improvement using statistical
techniques. Low cost solutions such as
overage reduction, providing access to
HTR (hard to reach) areas, handling
rejection reduction, etc. are
implemented. |
|
 |
|
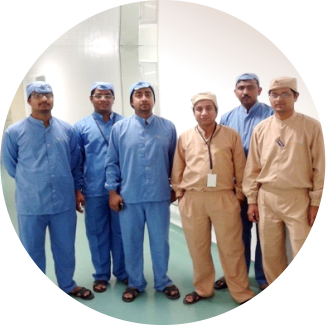 |
|
|
|
Curbing Losses, Yield Benefits: |
Role Model team, Formulations Hyderabad Plant 3 took up a project for improving the
yield of Fexofenadine 180 mg Tablets at manufacturing stage, which was at 94.8%
(average for FY14). Detailed process mapping and data analysis indicated that most of
the yield losses occur at granulation, coating and compression stages. The actions
taken include: |
|
Granulation stage: |
Fixing of vent filter to Rapid Mixer Grinder and
automating milling process. |
|
Compression stage: |
Optimising material usage. |
|
Coating stage: |
Replacing compressed air lines with larger
inner-diameter air pipe to facilitate better spray
pattern, and replacement of inlet air filters of
coating machine for maintenance of bed
temperature. |
|
Other Examples |
Apex Predator Lions Team improved product yield of
Metoprolol common over-coated pellets for 25, 50, 100
and 200 mg strengths of ER tablets from 97% to 99%
(7.61 kg/batch). |
|
|
Major impacting solutions were: Lower strength division at blending and compression stages, optimised coating parameters at sustained release stage.
This resulted in generation of lesser sub-standard size pellets thereby increasing
the product yield. |
Financial benefits - ₹3,200,000 annually. |
|
Dreamwalk Team optimised overages of coating solution used at extended release (ER) coating stage for Dipyridamole Extended Release and Acetylsalicylic Acid Capsules thereby reducing material costs. A detailed analysis of weight build-up for drug coated pellets at 70.82% and 82.30% was performed. The results established that the ER coating solution can be reduced from 484 kg to 387 kg, thereby optimising coating material overages at ER coating stage from 40% to 12%. |
Annual savings from the project - ₹1,400,000. |
|
Micro Bullets Team in QC optimised the turn-around time of analysis by altering the preparation of microbiological media like Soyabean Casein Digest Agar Media (SCDA) from daily to once in ten days by validating the hold time. An in-line analysis with pharmacopeia requirements was conducted and it was concluded that the media can be used for 10 days during routine usage. Apart from resulting in work simplification and saving of man-hours, it also reduced cost by 90%. |
Annual savings from the project - ₹1,168,700. |
|
|
|