|
|
|
CONTINUOUS IMPROVEMENT |
CONTINUOUS IMPROVEMENT AT WORK |
|
People Productivity |
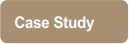 |
|
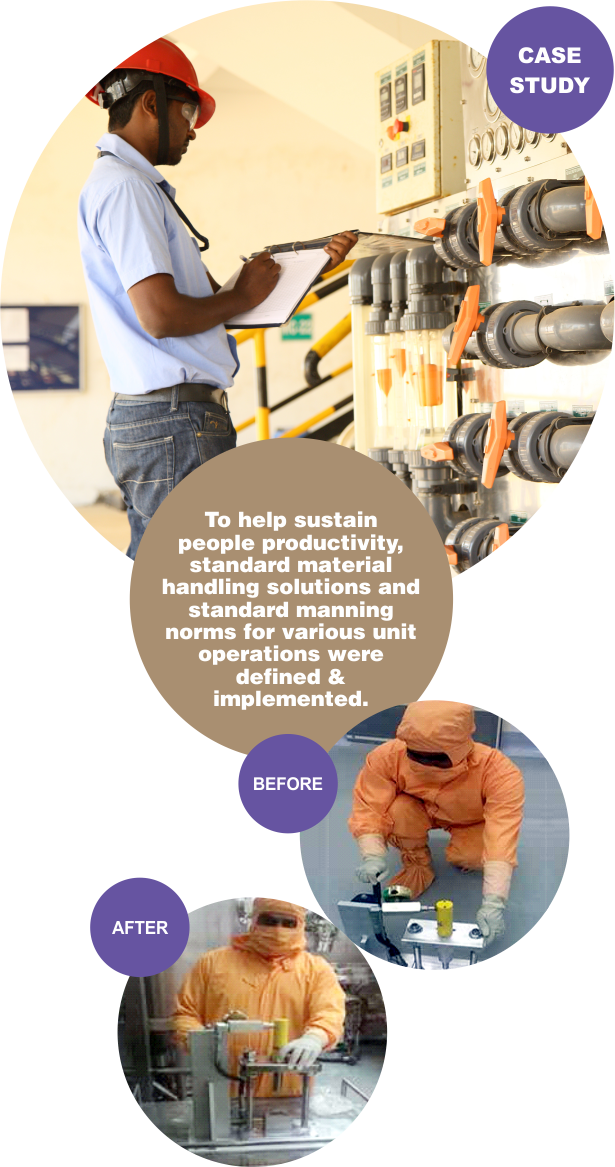 |
|
Making the MOST
of the Resources |
CHALLENGE |
To increase shop floor productivity by providing a comfortable and safe work environment to the workforce. |
|
INTERVENTION |
At each plant, a core team was identified, trained and certified on MOST by UMAS (external consultant). Detailed process description and activity mapping for each unit operation (included in the scope of work) was prepared. Direct observations and data of tasks carried out on the shop floor was entered into MDAT software. Based on the results, action plans were formulated in consultation with the teams, roles were re-defined wherever necessary and new control procedures were established along with periodic reviews to ensure institutionalisation. |
The recommendation from MOST study included; automation, mechanisation, and rationalisation of work. |
|
OUTCOME |
 |
Enriched work content and higher engagement due to better ergonomics and elimination of non-value added movements |
|
|
 |
Significant improvement in ergonomics |
|
|
 |
Manpower savings - up to 20% |
|
|
|
|
|
|
|
|
|
|
|
|
|
|
|
|
|
|